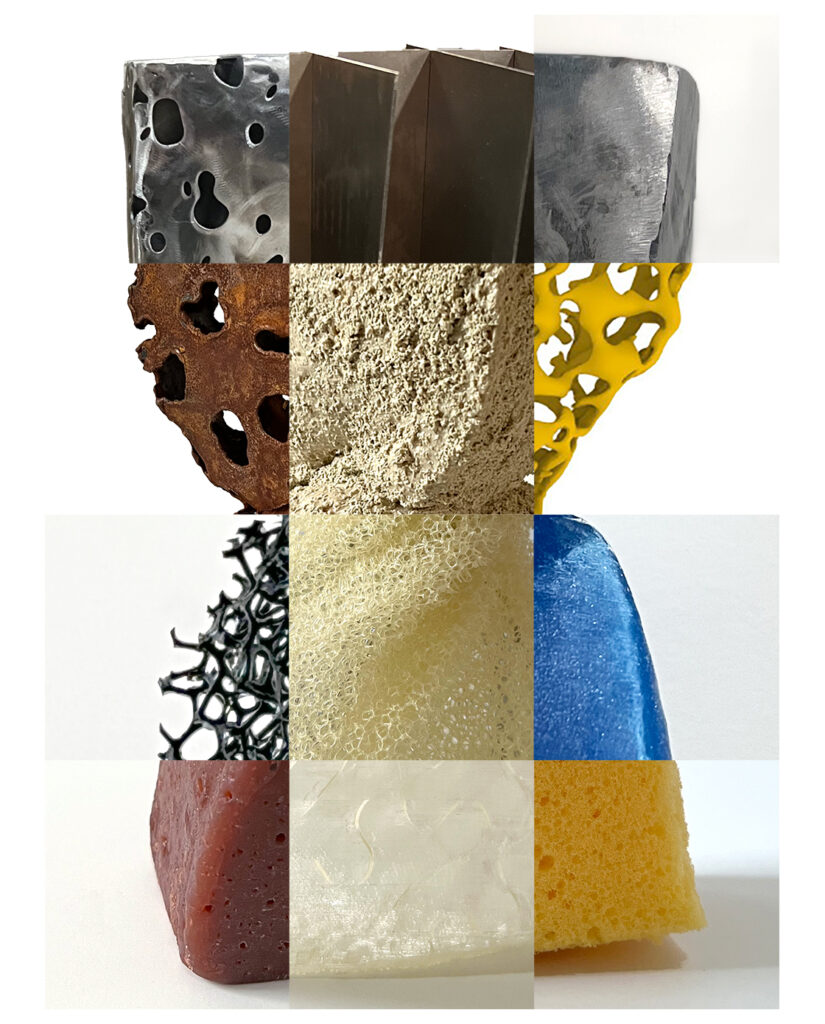
SPONGE MODELS
I explored a wide range of materials and processes during the first year of the Works in Public Program. Each of these models contributed in one way or another to the final prototype / maquette.
3D transparent PLA print
This was the model I used on my Works in Public application.
The inner filaments created a nice texture, similar to a sponge, and the translucency was ideal.
Initially I thought the large- scale sculpture could be printed using recycled PLA filaments, or crushed PET water bottles. I insisted on keeping some sort of transparency so that I could visually capture the flow of water.
Wax model
I used the above 3D PLA print to create a silicon mold, and with it casted this model in wax. The shape is the same, it only has a new, manually carved, texture.
This model was incredibly helpful. On one hand, it helped visualize how a solid, hand-carved porous texture would look like– prompting the option to explore fabrication using EPS foam. And on the other hand, it was used to map out planes for the metal prototype.
Tinted resin
This model revived the possibility of some sort of transparency, which I always coveted. However, it would have involved creating a large mold and casting using a huge amount of plastic. Even if adding fillers or objects like water bottles, the fabrication costs were above budget, and I would have hated using that much plastic. This model became the sculpture “Iceberg Hourglass”.
Sand model
A sand-mix coated model. This introduced the option to use sand or concrete as the primary material for the sculpture, given the strong connection with the hourglass’ time measurement.
The silhouette is slightly different than the previous models since it didn’t use a mold; the mix was added to an aqua resin coated twisted sponge.
Black stipple sponge
This little twisted stipple sponge turned out to be a break-thru and at the end, the visual reference I would select for the final direction. I explored doing a large open-cell structure and imagined it being done in metal.
This model fascinated me and it was the inspiration for several drawings, including the Hourglass Concept Drawing.
A Digital Option
This rendering was based and inspired by the small stipple sponge models and some of my hourglass drawings. The rendering, done by consultant Robert Wrazen, would in theory allow to print the large-scale sculpture in metal or in sand. Either option was out of budget.
This digital model introduced the idea of a hollow sponge – the design would allow to see through the cavities.
Metal Model
Following the digital drawing, I wrapped the wax model using aluminum foil and marked all the different planes. The 10 stretched planes were enlarged, printed and then used as stencils to cut on metal sheet.
Before bending and welding I drilled the metal sheets and enlarged the holes with a plasma cutter.
Metal Prototype I
For the first prototype, Haksul Lee created a 3D drawing in Rhino based on the Wax Model.
Following the same logic as in my first model, but now with digital files, the planes were laser cut on A36/1008 Mild Steel (.059″). This was a complicated assembly due to the small size (8 ½ “tall), angles, and mid “twisted” section.
Metal Prototype II
We sent a second set of cuts to SendCutSend, this time larger. This prototype was equally challenging to put together despite the larger size; we realized we had to change the fabrication plan. We needed to incorporate some sort of guide or reference so that all pieces could meet perfectly, keeping all angles and curves.
For the texture, I drilled the holes onto the welded piece and plasma cut it as well, but that also didn’t work well, the openings would need to be drawn into the Rhino file.
Metal Prototype III
The new fabrication plan consisted of adding an armature inside to serve as primary support and to help match and align all planes. I drew all opening holes into the Rhino file, and a new cutting plan was created.
The assembly was significantly easier and solid; it was this file that was shared with Brandywine Valley Fabricators for final production.